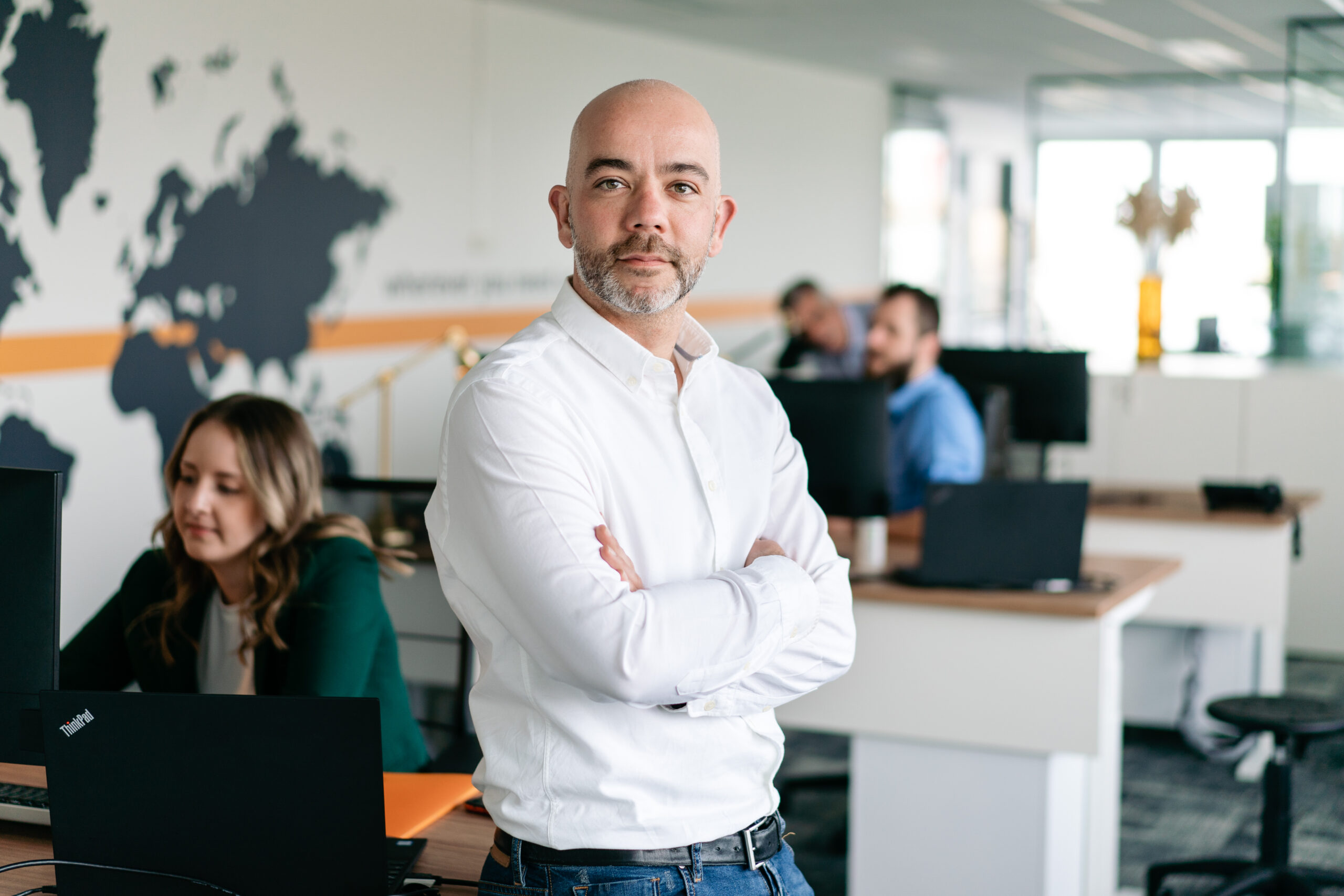
Kenneth de Paepe is set to succeed Roeland Wegman as Managing Director of Köttermann B.V. on 30 June 2025.
As of 30 June 2025, the Köttermann Group will see a leadership change at its Dutch subsidiary, Köttermann B.V.: Roeland Wegman will step down from his position as Managing Director. The Köttermann Group thanks Roeland Wegman for his dedication and contribution to the management of the Breda site. “We wish him all the best for the future, both personally and professionally,” says Kazim Doyuran, Managing Director of Köttermann GmbH and the Köttermann Group.
Kenneth de Paepe has been with the Köttermann Group for many years and has successfully led the Belgian subsidiary, Köttermann bvba – also responsible for Luxembourg – since 2018. A seasoned industry expert, he brings extensive market knowledge and strategic insight to the role. “I am very much looking forward to this new role in the Netherlands and to strategically expanding our activities across the Benelux region together with the local team,” says Kenneth de Paepe. “Köttermann stands for quality, safety and tailored solutions, values I am committed to further strengthening across all three countries.”
“The Benelux region is a key growth market for us. With Kenneth de Paepe, we have an experienced leader who will consistently pursue our strategic goals, business development strategy and actively connect our sites across all three countries,” adds Kazim Doyuran. “Kenneth has a proven track record in Belgium, having successfully grown the business while continuously striving to deliver better solutions in the field of laboratory infrastructure.”